Corrosion Detection in pipes with EMAT generated guided waves
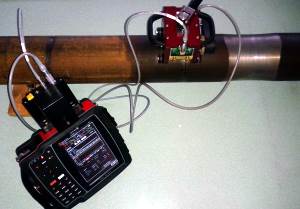
The aim of the project is to study abilities of medium range guided waves inspection technique (MRUT) using EMATs for detection and sizing of local corrosion in pipes. MRUT typically works with frequencies from 100 KHz to 1MHz, and can detect small pits (x10 more sensitivity than long range ultrasonic testing). MRUT is used in both attenuation and reflection mode to cover shorter distances (0.1-5 m). An ultrasonic wave is sent along the tube and reflects from defects ahead or behind the sensors.
This technique can be used for corrosion and crack detection on materials thinner than 13 mm.
An Ultrasonic Approach to Study the Status of the Green Energy Battery System
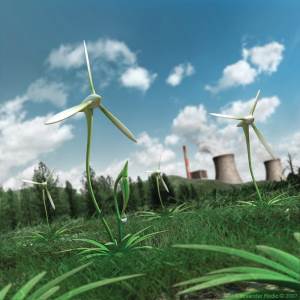
The renewable energy sources have an important role for the future of our planet and for the long-term security of the deliveries of electrical energy for the human race. The last events point out that exactly in these days – with crisis in the deliveries, exploding energy prices and global changes in the climate – more than every time it is necessary the using of alternative energy sources. Where does green energy come from? The most important sources are solar energy and wind energy. Common feature of all sources of green energy is that the batteries are used to store energy. Adding the lately very intensive work on the creation of electric cars, it is explained very great importance of the batteries. The need for inline analysis of the current state of devices for energy storage has increased in recent years; in this connection it is important to continuously monitor their status.
The project has studied an ultrasonic measurement of the density of battery electrolyte depending on the ambient temperature range from -20⁰C to +40⁰C. It is a feasible and effective approach, and can be used to monitor the density of lead-acid battery electrolyte and from there to automatically register condition at any time. This system can also achieve a variety of additional functions simultaneously, such as voltage measurement, current measurement, level measurement, stratification, data storage, data conversion. It can facilitate the on-line monitoring and intelligent management of the battery running state.
The major advantages of the method are: real-time; high accuracy; small size; on-line monitoring, and high reliability. The velocity measured by this method can reach a relative accuracy of ±0.2%, and it can reach a measurement accuracy of 0.001 g/cm3 by converting velocity to density. Since the batteries are usually positioned on awkward places it is offered an opportunity for distance measurement by means of radio signals.
Optimal Conditions for Electrospinning of Defect-Free Polyvinyl alcohol Nanofibers

The goal of the project is to obtain smooth, homogeneous and defect free nanofibers from Polyvinyl alcohol (PVA) solution by electrospinning. Electrospinning is a process that creates nanofibers through an electrically charged jet of polymer solution or polymer melt. It is a relatively easy and perspective method for producing polymeric, ceramic and composite fibers, which may vary from several nanometers to several micrometers. Project activities cover development equipment for electrospinning, experimental work for determination of optimal conditions for electrospinning of defectfree nanofibers and analyzing their morphology, structure and qualities.
Centre for Education and Training in NDT and Production Quality Control at The Technical University of Sofia
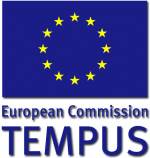
Tempus project S_JEP 09299
Creation of a "Centre for NonDestructive Testing Education and Training in Production Quality Control" to be located at the Higher Institute of Mechanical and Electrical Engineering in Sofia. In close collaboration with the Higher Institutes of Mechanical and Electrical Engineering at Varna and Plovdiv, this centre will run a twoyear postgraduate programme in NDT, some basic NDT courses for graduates, and some NDT courses within the framework of existing undergraduate programmes in Mechanical and Electrical Engineering.
Production line integrated sensor system for porosity QC of magnesium diecastings
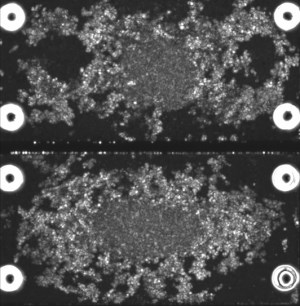
Project Acronym: MAGCAST
The Magcast project is a European initiative to develop digital radiography of Magnesium casts. This multi-million Euro project involves companies & research orgnisations from across Europe, including experts in digital radiography, x-ray tube manufacturers, NDT specialists, software engineers and Magnesium casting manufacturers. The final product will be integrated into Magnesium casting process lines. Advanced defect detection software will examine the digital radiographs for faults such as porosity, and will provide real time feedback for SPC and Six Sigma purposes. The system can be configured to automatically modify the process, if the standard of castings falls below a preset level. The aim of this system is to improve the quality of Magnesium castings, provide real time digital radiographs for QA, and to eliminate unnecessary waste of materials and time.
Magnesium alloys are approximately 60% lighter than LM24 aluminium casting alloys and 80% lighter than steel. However, despite the tremendous advantages offered by Magnesium castings, their use in various industries is being hindered by the difficulty of casting Magnesium components of consistently acceptable quality due to internal porosity - particularly in thin walled, and complex shaped castings.
Internal porosity is a problem in itself and is also the main determinant of the structural integrity and corrosion resistance of the components. In continuous production, the problem is in controlling the casting process to consistently keep porosity to an acceptably low level. This requires a system capable of rapidly detecting and quantifying internal porosity in cast parts. If a critical increase in porosity is not detected early enough, the manufacturing plant will incur high scrap and operating costs. This contributes to high component costs and a difficulty in satisfying demand for the mass production industries.
This project will overcome the problem by delivering a digital radiography system that will be fully integrated with a casting production line. The result will be an ability to rapidly detect an out of control process, with respect to porosity, and hence improve real-time control. This will enable the system to intervene rapidly in a continuous casting process, to restore control before the production of large quantities of scrap.
This project has received funding from the European Union’s Fifth Framework Programme for research, technological development and demonstration under grant agreement no G5ST-CT-2002-10563
Development of a robotic system for the inspection of aircraft wings and fuselage
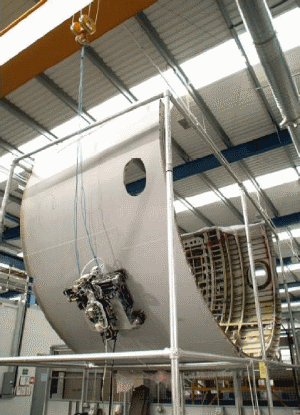
Project Acronym: ROBAIR
Regular and periodic non-destructive testing (NDT) is mandatory for civil airlines throughout the world. Most inspection is currently carried out manually, such that operator fatigue can lead to mistakes. Increasingly, airlines require a hard copy of inspection results to eliminate operator subjectivity. Furthermore, the requirement for 100 % inspection of vital structural features is becoming more commonplace and the slow rate of manual inspection is therefore prohibitively expensive. The cost of NDT is increased further where X-ray inspection is used, since components to be inspected must be removed from the aircraft.
As well as using conventional NDT sensors, the Robair project involved the development of the following technologies: acoustic camera, phased arrays, thermography, dry contact ultrasound and eddy currents. It was anticipated that the prototype system developed to be commercialised soon after project completion.
The objective of this programme was to develop a robotic inspection system, which would walk over large areas of an aircraft structure, carrying out automatic data collection and interpretation to identify all structural faws, without the need to dismantle components.
The output of the project was a robot designed to climb over the fuselage and wing areas of aircraft and inspect rows of rivets for loose rivets and cracks.
The vacuum adhesion climbing robot provides motion on aircraft wings and fuselage (mass = 20 kg). On-board control systems with tele-operation from an operator PC via a twisted pair. Flexible feet adjust to a range of surface curvatures. Vacuum sensors check for adequate adhesion before allowing robot motion before each walking step.
A 4-axis Cartesian scanner deploys NDT sensors (mass = 22 kg, end-effecter repeatability = 1 mm).
NDT of rows of rivets using ultrasonic phase arrays, ultrasonic wheel probes, eddy currents and thermography. For thermograhy, the scanning arm is removed and replaced by a thermographic camera and heat source. The design uses a hierarchy of universal joints in each foot, ankle and structure to provide the flexibility to different surface curvatures but yet remain rigid when attached to the surface.
This project has received funding from the European Union’s Fifth Framework Programme for research, technological development and demonstration under grant agreement no G4ST-CT-2000-50028
Train mounted sensors and systems for the inspection of rails
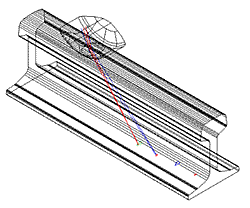
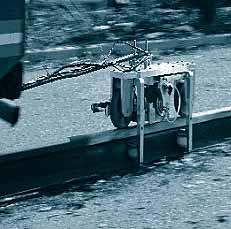
Project Acronym: RAILINSPECT
Description: Train-mounted sensors and systems for the inspection of rails.
- Automated NDT to cover whole of rail head and web
- Scanning with test vehicle travelling at 80km/h
- Ultrasonic, eddy current and magnetic flux leakage being evaluated
This project has received funding from the European Union’s Fifth Framework Programme for research, technological development and demonstration under grant agreement no G3ST-CT-2001-50169
Development of a novel non-destructive testing techniques and integrated online process control for robotic and flexible FSW systems
Project Acronym: QUALISTIR
Description: Actual welding techniques have a negative impact for (1) danger to operators due to presence of poisonous fumes, (2) labour intensive with certified operators, and (3) high costs due to manual work and rework. Friction Stir Welding (FSW) allows to reduce the scraps (about 15%). Moreover, lightening the weldings, it reduces all type of transport costs. FSW (invented 1999 by TWI-The Welding Institute, RD Tech partner in this project) has the potential to overcome the above mentioned limitations, but itself has still some limitations that QUALISTIR is aimed to overcome: (i) Actual in-line Non Destructive Control monitoring techniques are not able to detect "kissing" bonds, due to unmonitored fluctuation of the welding parameters or welding in adverse conditions. (ii) Actual NDT techniques are made on long-straight welds, but the application of FSW can drastically increase if the process could be carried out by a flexible multi-position friction stir welding system incorporating robots and gantries.
This project has received funding from the European Union’s Fifth Framework Programme for research, technological development and demonstration under grant agreement no G4ST-CT-2001-50117
Development of a robotic system for the inspection of large steel/aluminium plates in industrial plants
Project Acronym: ROBOTINSPECTOR
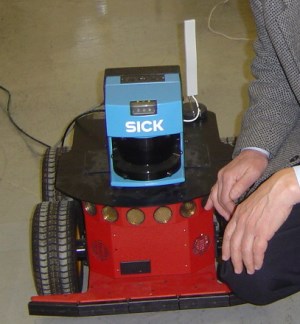
Description: The aim of Robot Inspector is to develop a semi-automated inspection vehicle for measuring plate thickness and detecting corrosion and cracking in the plate or welds between plates. One of the main target application areas is the inspection of storage tank floors.
The project combines ultrasonic and ACFM inspection tools, all deployed from the one robotic crawler. The partners include companies experienced in software, robotics and positioning systems as well as NDT, from a range of European countries, working in collaboration.
This project has received funding from the European Union’s Fifth Framework Programme for research, technological development and demonstration under grant agreement no G1ST-CT-2002-50183
Development of new and novel automated inspection technology for glass reinforced plastic wind turbine blades
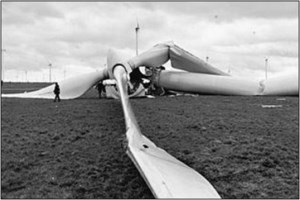
Project Acronym: RENEWITT
Europe has set ambitious goals for minimising dependence on fossil fuels and reducing greenhouse gas (GHG) emissions. Similarly, a growing percentage of European consumers savvy to the benefits of alternative forms of energy supports the development and installation of facilities that provide renewable energy.
As such, the market for electricity generation harnessing the power of wind is growing. In order to meet the expected demand, wind turbine blade (WTB) manufacturers have turned to glass-reinforced plastics rather than metal to increase the size and output of the wind turbines while saving on cost and weight. However, suitable non-destructive testing (NDT) techniques for rapid and accurate inspection of very large areas are lacking, resulting in increased manufacturing and maintenance costs as well as downtime.
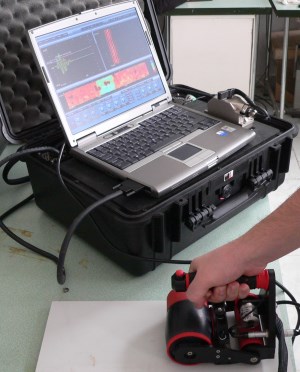
The EU-funded ‘Development of new and novel automated inspection technology for glass reinforced plastic wind turbine blades’ (Renewitt) project was initiated to develop the necessary NDT techniques in order to enable European WTB manufacturers to use the optimal materials with cost savings. Thus, the project sought to maximise the efficiency of WTBs while increasing the competitiveness of European WTB manufacturers.
The Renewitt project team successfully developed four NDT techniques for application to glass-reinforced plastic WTBs, enabling early detection of defects or damage. First, the researchers applied digital radiography which has revolutionised the field of X-ray imaging using digital sensors instead of traditional radiographic film. They also applied laser shearography, extending its conventional capabilities for out-of-plane deformation and enabling in-plane detection as well. The investigators also used pulsed thermography that essentially relies on a brief pulse or flash of energy applied to a surface and subsequent detection of non-uniformities during cooling. Finally, the team employed two different types of ultrasound detection.
The researchers incorporated all of these NDT methodologies into a single system that was software controlled and mounted on a robot scanner to produce the Renewitt WTB inspection system. The system is capable of reaching all areas of the blade, is operated by a single technician and is applicable during both the manufacturing and the maintenance processes.
In summary, the Renewitt project developed the necessary NDT methods for inspection of glass-reinforced plastic WTBs and the means to apply them. Commercialisation of the technology has the potential to significantly enhance the competitiveness of Europe’s WTB manufacturers while reducing GHG emissions and Europe’s dependence on fossil fuels.
More information: ReNewIt Project
This project has received funding from the European Union’s Sixth Framework Programme for research, technological development and demonstration under grant agreement no COOP-CT-2003-508600
Quality assurance and structural evaluation of GRP pipes
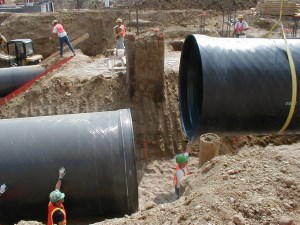
Project Acronym: SURE2GRIP
The ultimate aim of the SURE2GRIP project was to develop novel non-destructive evaluation (NDE) techniques, sensors and systems capable of assessing the quality assurance and structural integrity of the 'production' and 'in-service' glass-reinforced plastic (GRP) pipes and pipe joints. This key enabling technology would facilitate the use of GRP materials without the need for cost-prohibitive engineering processes such as secondary containment 'over-wrap'. The highly reliable and sensitive NDT methods developed would also expand the use of GRP pipe into other applications that were traditionally the domain of corrosion-prone metallic that resulted in a series of catastrophes.
The scientific and technical objectives of the project were the following:
- significantly develop and improve NDT techniques so that GRP pipe and joint defects such as 'kissing bonds' (KBs) are detected early in the production process;
- conduct inspections faster and hence reduce maintenance downtime by automating NDT techniques;
- deliver NDT techniques, validated in their individual areas of intended use;
- increase accuracy by eliminating operator subjectivity, increase safety and reduce instances of failure.
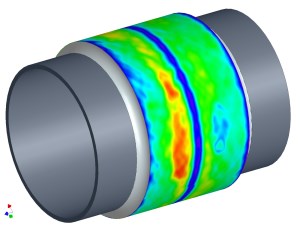
SURE2GRIP resulted in the following major achievements:
- a set of 6- and 12-inch pipe samples was designed and produced covering the main types of joints. Artificial defects were produced in the samples to mimic the types and sizes of defects sought.
- research was carried out into the use of radiographically opaque adhesive additives to enhance the detect joint defects.
- a low-energy digital radiography system was designed and built.
- a dual laser shearography system capable of separately resolving in-plane strain was developed and produced.
- a pulsed thermography system was built using an advanced flash excitation system.
- a feasibility study into the use of Lamb waves to detect and stimulate thermal emission from defects was carried out.
- a phased array ultrasonic system capable of rapid large area coverage using very little water was developed.
- a robotic scanner capable of carrying and controlling the thermography, phased array ultrasonic technology (PAUT) and radiography systems was designed and built.
- the above systems were integrated with the scanner to produce the SURE2GRIP GRP pipe inspection system.
More information: http://www.ndt.net/article/ecndt2006/doc/Mo.2.6.3.pdf
This project has received funding from the European Union’s Sixth Framework Programme for research, technological development and demonstration under grant agreement no COOP-CT-2004-513266
Development of novel digital radiography technology to facilitate the "traditionally less research intensive inspection industry sector" change from manual film radiography to automated digital radiography
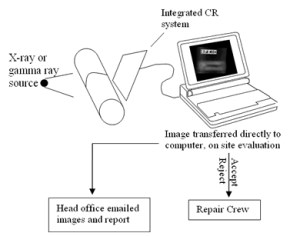
Project Acronym: FilmFree
The objectives of the FilmFree project are to make a number of technological advances that will take the digital industrial radiography sector into a new era to effectively replace film as the detecting media. SME's will play the major role in this development and as a result they will make significant commercial gains and growth from the digital radiography market place both within Europe (estimated at 400million Euros annually) and globally (estimated at between 1bn and 1.25bn Euros).
Medical digital radiography is totally unsuitable for industrial use because it cannot operate at the X-Ray energies required to examine engineering materials and metals, nor can it attain the image quality required to find the defects that could ultimately lead to the catastrophic failure of a safety critical component in service.
The lower technology NDT (Non Destructive Testing) service inspection companies, are mainly SME's supplying labour intensive inspection services at low margins to traditional industries (e.g. engineering fabrication industry and the rail industry). There are about 2000 of these companies in Europe and they will benefit from the technology advances made in FilmFree by being able to upgrade their services to include digital radiography an d thereby gain access to higher value added sectors such as the petrochemical and oil & gas markets.
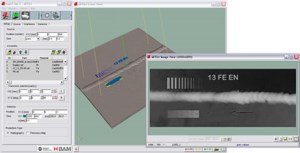
Similarly the European higher technology digital radiographic equipment suppliers (SME's) will gain a competitive advantage over the small number of Large Enterprise companies that dominate the global market from the USA and Japan. An estimated 10,000 industrial radiographers are exposed to a high risk of radiation within Europe. FilmFree will significantly reduce the risks faced for the majority radiographers. Also a minimum of 50% reduction in radiation exposure time is expected during the 25 million annual working hours of radiographers.
More information: FilmFree Project webpage
This project has received funding from the European Union’s Sixth Framework Programme for research, technological development and demonstration under grant agreement no NMP2-CT-2005-515746
Development of novel digital computed radiography technology using high energy radiation for the volumetric examination of large scale components
Project Acronym: HEDRAD
HEDRad will produce a new and novel, mobile high energy digital computed radiography system that will allow new applications by extending the range of energy levels that can be currently applied to phosphor screen computed radiation detectors in site applications.
Strategic Objectives
- To develop a technique applicable to power plant, chemical plant and other heavy industries requiring similar Non Destructive Evaluation.
- Make possible in-service inspections of thick sections which normally involve downtime.
- Develop competitiveness of SMEs involved in the project
Technical Objectives
- Development of prototype portable computed radiographic system capable of operating at high radiation energies that will include an enhanced computed radiographic scanner and reader system.
- Produce a Data Fusion Software to produce high quality images by increasing the Signal to Ratio (SNR).
- Development of digital radiographic techniques for the examination of large thick section components to meet the needs of a number of energy related industries. The technique development will include examination in thick section casting and also the functional assessment of the internals of thick section components such as pumps and valves.
More information: HEDRAD Project webpage
This project has received funding from the European Union’s Seventh Framework Programme for research, technological development and demonstration under grant agreement no FP7-SME-2007-1-222240